This website uses cookies so that we can provide you with the best user experience possible. Cookie information is stored in your browser and performs functions such as recognising you when you return to our website and helping our team to understand which sections of the website you find most interesting and useful.
Contract manufacturing of textile laser cutting
The Laser 3XL Conveyor impresses right from the start. The non-contact cutting achieves high dimensional accuracy with a perfectly welded cutting edge. Even complicated shapes can be implemented easily.
But as we all know, pictures and videos say more than 1000 words, which is why you can see for yourself the power of our Laser 3XL Conveyor in this video.
See our textile laser live in action!
Advantages of laser cutting fabrics
- Time savings: Laser cutting speeds up fabric cutting significantly compared to traditional methods.
- Quality assurance: The synchronous conveyor technology ensures consistently high quality
- Repeatability: This leads to more consistent products, especially in mass production.
- Contactless method: The fabric is not touched directly, reducing maintenance and wear and increasing efficiency. This means there is no distortion of the fabric.
- Reduced post-processing: The laser seals the edge of the fabric as it cuts, preventing fraying and requiring fewer post-processing steps.
- Cut-and-seal process: Hot-melted, clean and frayed cut edges save work steps during further processing
- Textile-friendly work: Every cm of the material to be cut is used and precise cutting of complex patterns or templates also works easily with digital cutting patterns.
Questions and answers about laser cutting of textiles
An operator calls up the digital cutting in the processing program and starts the cutting process at the push of a button. After automatic unwinding, the fabric or textile to be cut is placed flat on the processing surface of the laser machine and sucked in and fixed using a vacuum.
One person monitors the process and either removes the finished cut parts directly from the table or sorts them from the collection container set up at the end.
For example, the software integrated into the laser ensures the exact positioning of the laser head and thus enables perfect laser cutting of fabrics based on the cutting file.
Fast and reliable processing of inquiries and orders is part of the success story in our 40-year company history.
The laser works with front-end software to control and control the laser system.
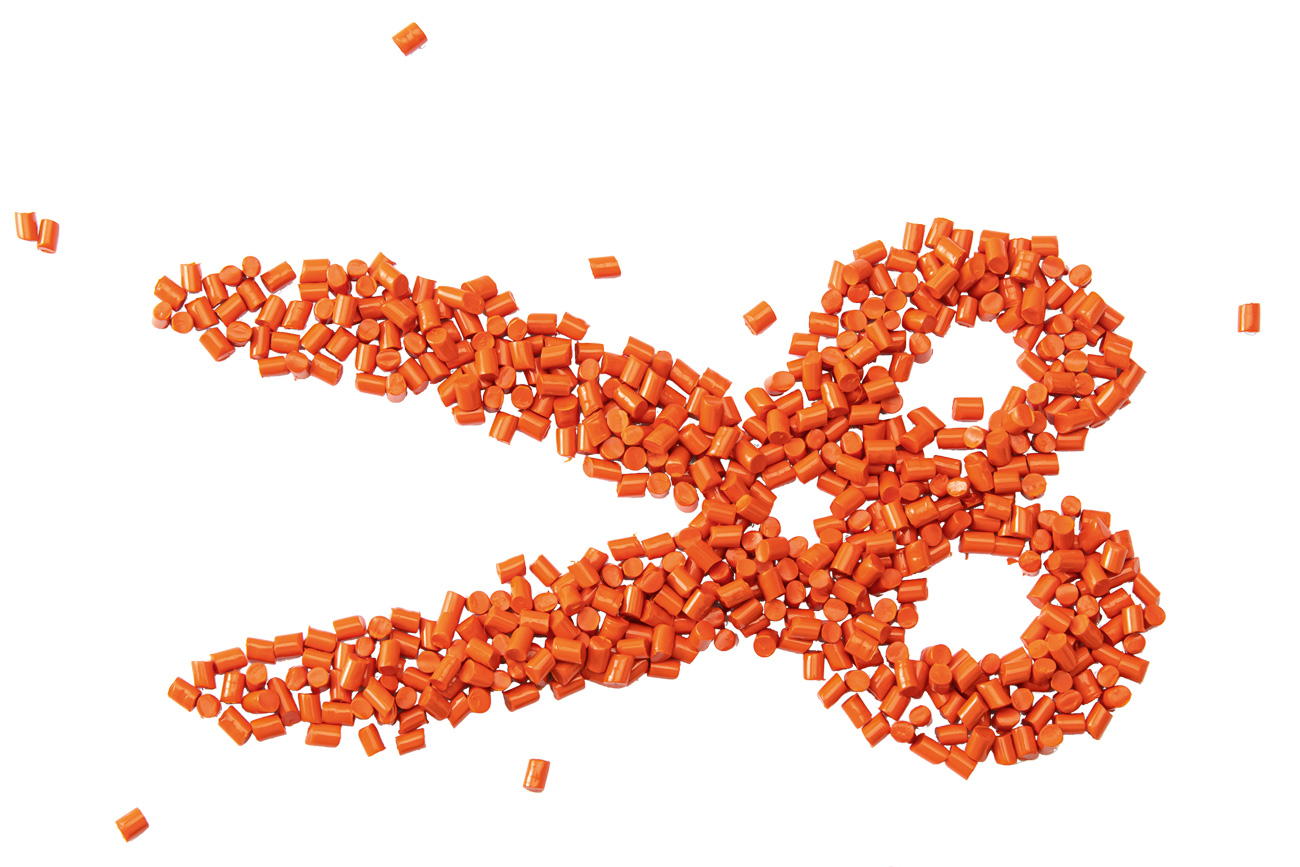
Areas of application of our laser cutter
Military clothing
Protective clothing
Advertising technology (e.g.: flags)
Upholstered furniture
Automotive
Acoustic and sound insulation (interior construction)
Filter materials
We make it fit– since 1984
Since 1984, A.B.S. produces a variety of silo variants that offer customers endless options for storing bulk goods.
The founder’s idea back then was to use textiles instead of metal to build silos – just as stable and resilient, but significantly more sustainable and flexible. A design that was able to establish itself: today the name A.B.S. worldwide for high-quality, flexible silos with a service life of decades, used successfully around 100,000 times in industry, agriculture and in wood pellet storage.
With individual solutions tailored precisely to your requirements, we make it suitable – guaranteed.
Our specialty is tailor-made solutions for all bulk material handling issues relating to the storage, conveying, dosing or discharge of bulk materials. We rely on technical expertise through 3D planning and the use of the Euolaser, even for very large cuts.
Benefit from our approximately 40 years of experience as a manufacturer and planner, because this makes us a reliable production partner for our customers.
If you have any further questions or uncertainties, we are always there for you! Please feel free to ask us, we look forward to making you an individual offer!