This website uses cookies so that we can provide you with the best user experience possible. Cookie information is stored in your browser and performs functions such as recognising you when you return to our website and helping our team to understand which sections of the website you find most interesting and useful.
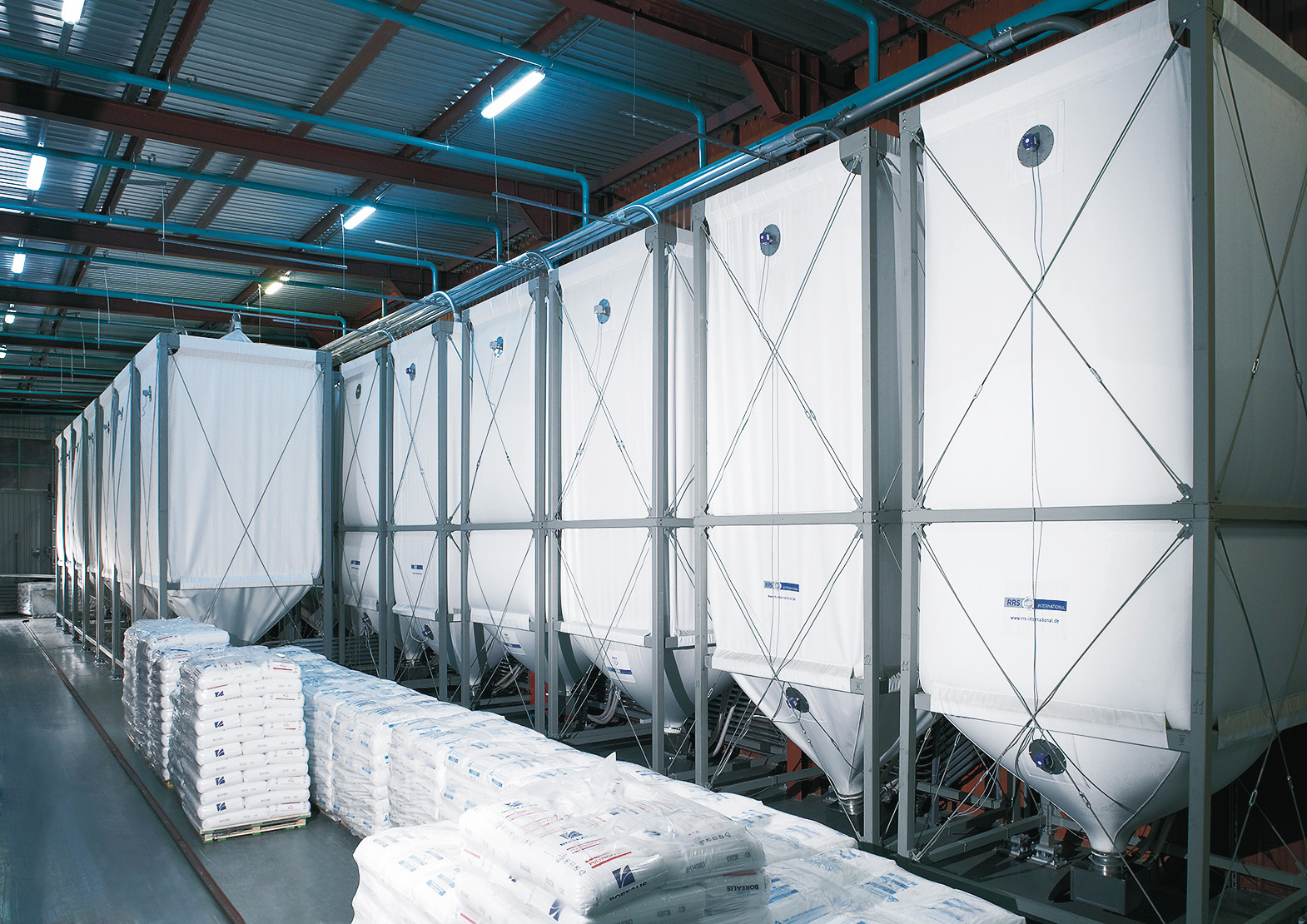
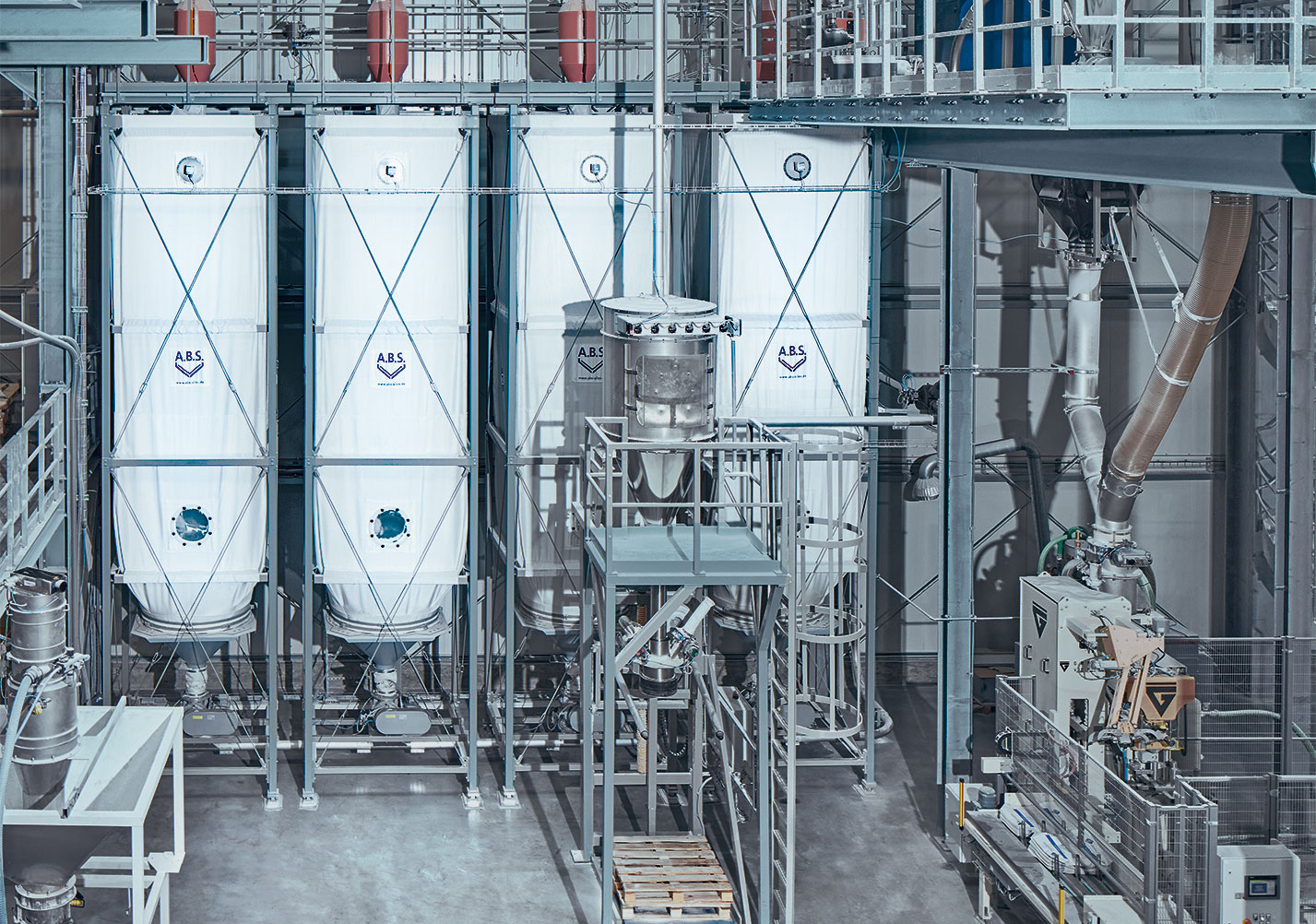
WE GET MORE SPACE FROM EVERY AREA.
A.B.S. FLEX SILOS FOR INDUSTRY
Available in square or rectangular shapes and in any required size, they ensure optimal use of the available space. And unlike metal silos, they can also be installed in places that are difficult to access. The high-strength and resilient TechnoTex fabric is specially tailored to the respective bulk material. Even the most demanding and sensitive applications are possible, e.g. B. in the food or chemical sector.
And last but not least, A.B.S. are convincing. Flex silos also have an exemplary price-performance ratio.
QUALITY INCREASE THROUGH IN-HOUSE STORAGE.
A.B.S. FLEX SILOS FOR INDUSTRY
Advantages of industrial silos
Gewebe ist exakt auf Schüttgut angepasst - z.B. un/beschichtet, lebensmittelkonform, elektrostatisch ableitfähig
Handhabung und Verwendbarkeit vergleichbar mit Metallsilos
7-fache Sicherheit auf Naht und Gewebe
optimale Auslaufeigenschaften - Siloform anpassbar an Anforderungen des Lagerguts
in quadratischer oder rechteckiger Form erhältlich - einpassbar an Ihre Räumlichkeiten
platzsparender Versand in Einzelteilen - kein Schwertransport
Sehr leicht zu reinigen
Sehr lange Lebensdauer
Kostengünstige Lagerung bei optimaler Raumausnutzung
Freie Wahl der Absperr- und Entleerorgane
Auslaufschwierige Schüttgüter können zusätzlich mit Austragshilfen ausgestattet werden
Auch an schwer zugänglichen Orten montierbar
TURNKEY COMPLETE SOLUTIONS WITH PLANT CONSTRUCTION FROM A.B.S.
Many different skills are required in plant engineering: consulting, planning, construction, assembly, service, know-how, expertise… A.B.S. combines all competencies.
We offer you complete turnkey solutions. It starts with an intensive consultation that looks at all the details of the respective project and finds the right solution. Because we look at the respective task holistically, we adapt the required control, filling level, weighing, conveying and dosing technology perfectly to the entire storage system.
Whether new construction, conversion or expansion of the system: From A.B.S. You receive a complete warehouse concept – from development, planning, construction and assembly to commissioning and service. Everything from a single source and everything with a system.




Clips of our silos for the industry
Application examples
Silos for industry.
Here you will find various silo projects for industry that have already been implemented.
PERFECT ALL AROUND: A.B.S. AT EUROCERAS
Internationally active: The wax specialist EuroCeras plant is located in Poland, between Wroclaw and Krakow. Here was A.B.S. responsible for planning, construction, assembly and control of a silo system for raw materials and finished products.
“With A.B.S. Everything is going very well to our satisfaction, everything works great. We will also contact you again for new projects.”
Helmut Keim, EuroCeras management
Learn more about the planning and construction of a silo system for raw materials and finished products at EuroCeras in Poland.
credentials
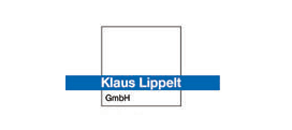
Klaus Lippelt
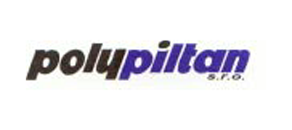
Polypiltan
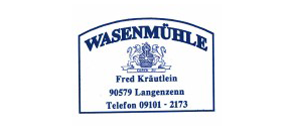
WASENMÜHLE
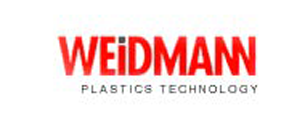
WEIDMANN
In Kędzierzyn-Koźle between Wroclaw and Kraków, a factory owned by the wax expert EuroCeras has experienced major expansion in the last 2 years, with the company A.B.S. Silo and conveyor systems played a decisive role. What started as a request for a few raw material silos became a complete project for a whole new system for handling the required raw materials and finished products.
In the original hall of the manufacturer of wax additives there are now two new plastic granulate silos from A.B.S. – Five more are installed in the new hall. All Flex silos are made of uncoated, high-strength and electrically conductive polyester fabric and hang in steel frames. They are each equipped with a level indicator, weighing technology and filter bags made of needle felt. While in agricultural silos and wood pellet silos made of fabric the silo lid was usually sufficient for filtering, here filter bags were necessary to increase the filter surface. This allows the conveying air to escape dust-free. The data from the four load cells of each Flex silo are evaluated in the control cabinet and the weighing result is displayed on a touch panel. These seven raw material silos serve as feed silos and ensure the material supply for the downstream process.
The effort required to transfer the bagged goods into these newly built storage silos is reduced to a minimum by using a fully automatic bag emptying station. The system empties the bags into a feed hopper. The plastic granules are then pneumatically conveyed into the selected flex silo at a rate of up to 12 t/h. The conveyor technology from the bag emptying station to the flex silos is designed according to the requirements.
The operator selects the flex silo to be filled and after simply pressing a button, a touch panel controls the filling process. After querying the full detectors, the pipe switches switch the conveying path to the selected flex silo and start the conveyor fan and the rotary valve. For filling, several flex silos can be selected and then filled one after the other. The switchover from one to the other Flex-Silo takes place automatically when the system is full. To do this, the rotary valve stops so that it can set the course for the next flex silo. Then the rotary valve starts again. If all full detectors in the selected silos are occupied, the filling process stops completely.
The filling of the 5 raw material silos in the new hall takes place over a long route through the outdoor area. The delivery line for the raw materials runs over 80 meters in a specially constructed pipe bridge to the flex silos in the newly built production hall. These pipelines are by no means left to their own devices. The pressure in them is constantly monitored. If the pressure reaches the limit range of the maximum pressure of the conveyor fan, the rotary valve stops. Now the delivery line can be blown clear again. If the pressure is back in the set working range, the rotary valve starts again. This monitoring reliably prevents the delivery line from becoming blocked.
The touch panel also controls the removal from the raw material silos. One or more silos are selected for removal and the pipe switches are then set accordingly. When the conveyor path is stopped, the material is released for removal by a vacuum conveyor. Through this, the granules are transported to two extruders and, after further processes, are finally processed in two spray towers.
After the spray towers, the finished product is transported via suction to 4 further A.B.S finished product silos. The separators used for this separate the processed product from the conveying air and have an output of 500-600 kg per hour.
Since the finished product, unlike the granules, is difficult to drain, assistance must be given when removing it. In order to avoid bridging and to ensure safe discharge, the A.B.S. finished goods silos are equipped with vibrating floors and vibrating motors. Rotary valves meter the product into the suction conveyor in the correct ratio to the conveying air and thus guarantee optimal flow conditions.
Using two powerful separators, which handle 4 to 5 tons per hour, the finished product is fed either to the BigBag filling station or to a fully automatic bag filling station.
The company A.B.S. Not only took over the planning, production and assembly, but also the complete electrical installation and control of the system.
The management Dr. It was not difficult for Puhl, Ms. Gross and Mr. Keim to place themselves entirely in the planning hands of A.B.S. to go. Initially they only planned to build some raw material silos at A.B.S. When they ordered, they were quickly impressed by their suggestions for planning an entire system. Thanks to good experiences from previous projects, they decided to hire process engineering experts after a short time and are very satisfied with the new system.